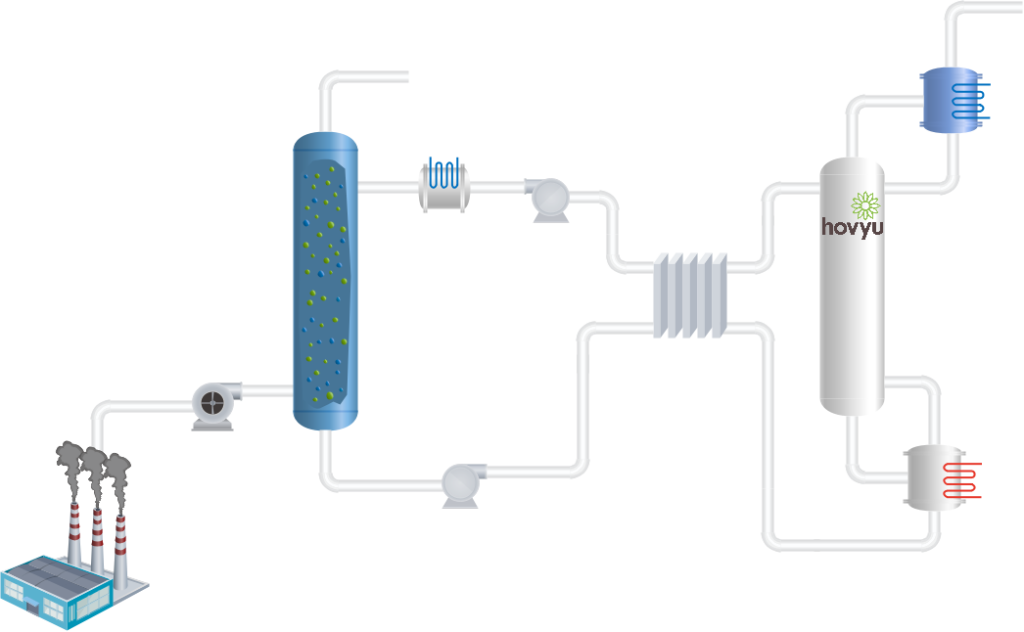
The principle
Amine-based process to capture CO2 work in a closed absorption desorption loop. The operating principle is based on a temperature swing where the absorption is taken at lower temperatures and desorption at higher temperatures.
In a absorber, the gas is washed with an amine solution (the solvent) where CO2 is selectively removed from the gas phase by reacting with the amine. The clean gas leaves the absorber while the solvent with the captured CO2 is sent to a regeneration section.
There CO2 is released by increasing the solvent temperature. The regenerated solvent is then cycled back to the absorber to remove more CO2 from the inlet gas while the produced CO2 is sent to
further processing (e.g., compression, drying and liquefaction) for its final use. For storage purposes, CO2 must have some specifications (see, for instance, Northern Lights requirements)
The temperature increase in the regeneration section is often provided by low pressure steam. The reboiler operates at temperatures around 120 °C. In this type of process, steam represents the major part of the consumables.
Solvent choice
The choice of the solvent plays a key role in the process performance. It will dictate the energy requirements as well as the solvent management strategies. Therefore, it will have a direct impact
on the plant design. A plant designed with one solvent is likely not be able to perform with other solvent. Therefore, the selection of an appropriate solvent should be considered from the start.
Traditional solvent for CO2 capture such as monoethanolamine (MEA) and CESAR1 (blend of AMP
and Piperazine) demands energy (in form of heat) typically ranging from 2.6 to 3.6 MJ/kg CO2.
Apart from low energy requirements, a solvent should also be stable. Flue gases contain several
other components than CO2. Oxygen, NOx and SOx are examples of components that can be present
in the flue gas and will have a direct impact on solvent.
Oxygen will react with the amine to form other components which eventually will decrease the absorption capacity of the solvent. Moreover, some of the components formed can leave the plant if
no proper emission control is in place. NOx and SOx are acid gases that react with the amine and accumulate in the solvent as they are not released in the regeneration section. They can also react to form other degradation compounds.
A good knowledge of the solvent allows the prediction of such compounds and the design of emission control techniques to safely operate such plants.
Emission Control & Solvent Management
Several strategies can be employed to avoid emissions of unwanted components, mitigation of
solvent degradation and its accumulation in the solvent. Water washes, acid washes, temperature
control and demisters are a few examples that could be implemented to control emissions.
The solvent degrades forming other components that accumulates in the solvent. Reclaiming
techniques are the used to clean the solvent and remove these compounds from the system.
Naturally, emission control and solvent management strategies will add operational costs to the
process. A good design and understanding of the process will keep the costs reduced while
maintaining the process performance.
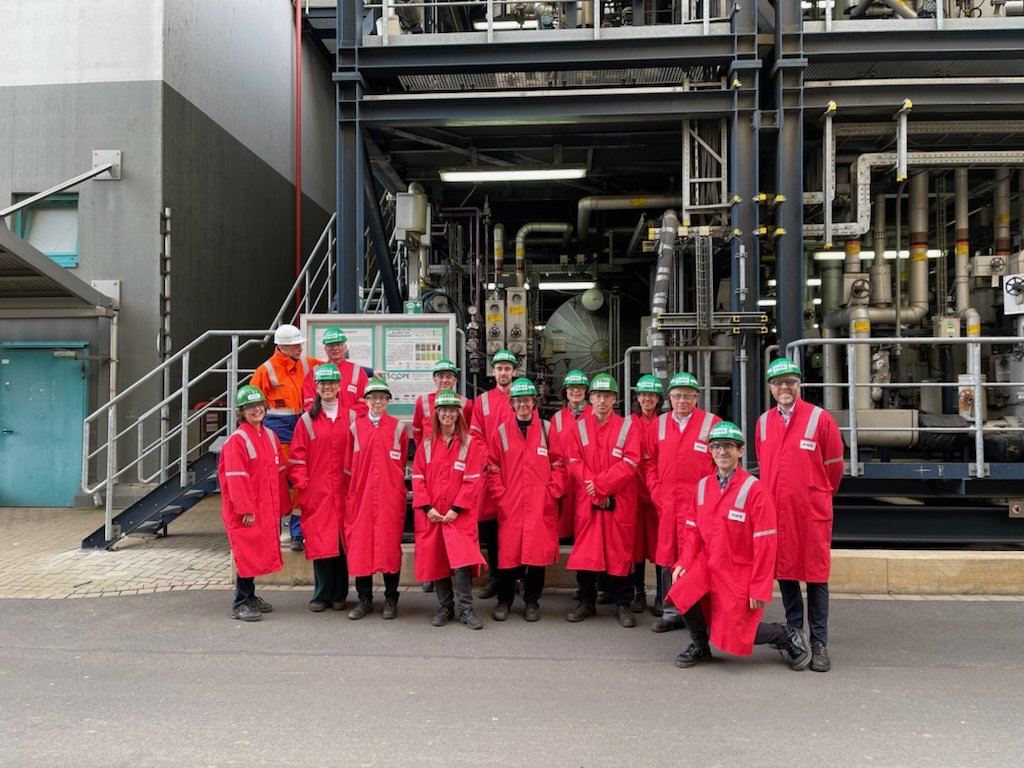